Die Produktion von Akkuzellen
Im letzten Artikel wurde beschrieben, wie sich unterschiedliche Zellchemien auf die Eigenschaften einer Akkuzelle auswirken. Die Entwicklung steht dabei noch am Anfang und man darf auf weitere sprunghafte Verbesserungen im Materialmix der Akkuzellen hoffen. Gerade jetzt kommen täglich Meldungen über angeblich revolutionäre Akkutechnologien, die den Markt neu aufmischen sollen. Diese Laborversuche zeigen oft vielversprechende Ergebnisse, die aber von einem massenproduktionsfähigen System noch Jahre entfernt sind. Laut Elon Musk reicht es nicht aus, eine neue Akkuzelle zu erfinden. Die eigentliche Herausforderung bestehe darin, die für einen Massenmarkt erforderliche Produktionstechnik zu entwickeln: „The machine, that builds the machine“. Damit lenkt er den Fokus vom Auto und von der Akkuzelle hin zur deren Fertigungsanlagen, in die er mindestens genauso viel Erfindergeist investiert.
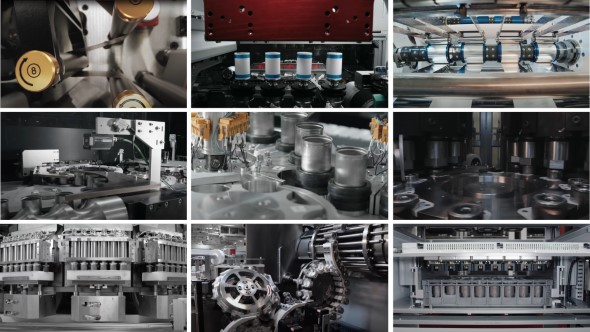
Bei der Herstellung einer Akkuzelle geht man von innen nach außen vor: Es beginnt bei den Elektroden (Kathode und Anode), geht über das Gehäuse und endet bei der „Erweckung“ zu einer aktiven Akkuzelle. Aber zurück zum Anfang: Das Trägermaterial der Elektroden ist eine Metallfolie. Bei der Kathode ist das in der Regel eine Aluminium-Folie (Kupfer würde hier korrodieren) und bei der Anode ist diese aus Kupfer (Aluminium würde hier mit dem eingebetteten Lithium reagieren). Diese leitfähigen Folien werden auf großen Rollen angeliefert (Mutter-Coil). Beim Betrachten der Maschinen, die diese Rollen verarbeiten, wird man zwangsläufig an die endlosen Bänder einer Papierfabrik oder einer Druckerei erinnert.
Auf die Folien wird das eigentliche Aktivmaterial aufgebracht – also der Teil der Zellchemie, der die Einlagerung der beweglichen Lithium-Ionen ermöglicht. Bei der Kathode handelt es sich meist um eine Kombination aus Cobalt, Nickel, Mangan oder Aluminium und das später als Ladungsträger dienende Lithium. Die Anode besteht meistens aus Grafit. Die genaue Zusammensetzung ist eines der Geheimnisse des Herstellers. Die Stoffe werden in Pulverform gemischt und mit einer Flüssigkeit in einem sogenannten Extruder zu einer schlammartigen Masse gepresst (Slurry). Während bei der Anode eine wässrige Lösung als Flüssigkeit verwendet wird, kommt bei der komplexeren Kathode noch ein Lösungsmittel zum Einsatz. An dieser Stelle entsteht ein Teil des Wasserbedarfes bei der Zellherstellung, für den die Lithium-Ionen-Akkus bekannt und berüchtigt sind. Gemäß Helmholtz-Institut liegt der Bedarf für einen 64 kWh Akku bei 3.840 Liter inklusive der Gewinnung der Rohstoffe. Allerdingt erreicht man diesen Wert auch durch den Verzehr von elf Avocados, 300 Gramm Rindfleisch oder 35 Tassen Kaffee – inklusive der Aufzucht der dafür benötigten Pflanzen und Tiere. Die Hersteller von Akkuzellen arbeiten kontinuierlich daran, den Bedarf weiter zu senken.
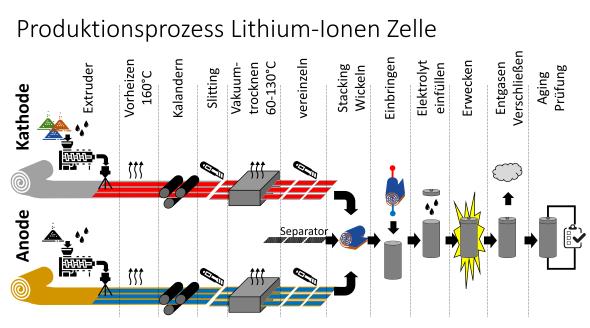
Mittels Spritzdüsen wird die Masse als gleichmäßiger Film beidseitig und in Bahnen auf die durchlaufende Trägerfolie gebracht. Das Verfahren erinnert an eine Druckerei, die den Text auf meterlange Papierbahnen aufträgt. Um die Haftung des Aktivmaterials zu gewährleisten, wird die so beschichtete Folie zunächst auf dem Luftkissen eines Schwebebahntrockners bei ca. 160 Grad vorgetrocknet. Anschließend läuft die Bahn durch einen mehrstufigen Walzprozess, bei dem mit bis zu 400 kg Pressdruck eine gleichmäßige Dicke mit hoher Dichte hergestellt wird. Man nennt diesen Prozess „Kalandern“. Erst jetzt wird die große Rolle (Mutter-Coil) in die später benötigten Bahnen (Tochter-Coils) geschnitten (Slitting). Eine Absaugung entfernt etwaige Verunreinigungen.
Im nächsten Schritt wird das auf die Trägerfolie aufgetragene Aktivmaterial durchgetrocknet. Der Prozess findet in einem Vakuum-Trockner statt bei einer Temperatur von ca. 60 – 130°C. Er dauert zw. 24 und 48 Stunden. Durch die Dauer, den Energiebedarf der Trocknung und dem Bedarf an Produktionsfläche ist dieser Schritt ein weiterer Kostentreiber bei der Herstellung von Akkuzellen. Viele Hersteller arbeiten daran, den Ablauf zu verkürzen und zu optimieren.
Nach der Trocknung werden die Bahnen je nach Zellform in die passende Form geschnitten. Getrennt durch eine Separatorschicht werden die Elektroden abwechselnd aufeinandergelegt: Das sogenannte Stacking, also Stapeln. Speziell bei Rundzellen nutzt man den Vorteil der Form und wickelt die Elektroden mit dem Separator dazwischen zu einer Rolle. Beim Schneiden der Trägerfolie der Kathode und der Anode wurden überstehende Fähnchen vorgesehen. Diese Tabs werden durch Ultraschall- oder Laserschweißen jeweils miteinander verbunden, um sie anschließend mit den Polen am Gehäuse zu verbinden. Der Stapel oder die Rolle wird in das Zellgehäuse in seine finale Position gebracht. Ab hier ähnelt die Produktionsanlage einer Abfüllanlage für Getränkedosen.
Nun wird mithilfe von lanzenförmigen Düsen der flüssige Elektrolyt in das Gehäuse eingefüllt, bis er die Elektroden vollständig umgibt. Nur der Separator trennt diese jetzt noch voneinander. Das Gehäuse wird soweit verschlossen, dass noch Gas austreten kann. Denn jetzt kommt der geheimnisvollste Schritt bei der Zellproduktion: Die Formation. Dabei wird die Akkuzelle zum ersten Mal geladen und entladen. In großen Regalen (Formierturm) werden dabei ganze Zell-Bataillone gleichzeitig behandelt. Das Verfahren lagert gezielt Lithium-Ionen in der Grafitschicht der Anode ein und es bildet sich eine dauerhafte Grenzschicht (SEI = Solid Elektrolyte Interface) zum Elektrolyten. Die Ausprägung und die Qualität dieses Vorgangs bestimmt maßgeblich die Leistungsfähigkeit, die Leistungsdichte und die Lebensdauer der Zelle. Deshalb spricht man auch von der Erweckung der Zelle als wäre es eine Art von Geburt. Der Prozess wird gesteuert durch kontrollierte Veränderung der Ladespannung, des Ladestroms und der Temperatur.
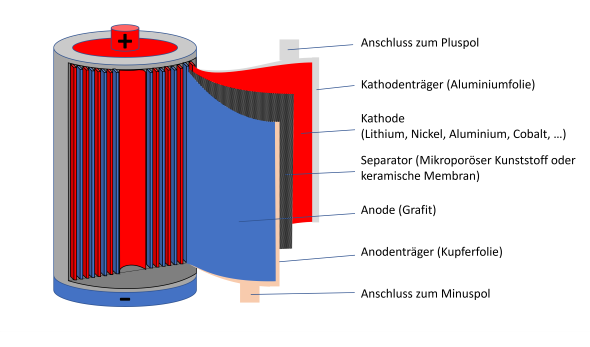
Während dessen wird der Elektrolyt erwärmt und gebildetes Gas tritt aus. Pouch-Zellen haben eine Gastasche, um das Ausgasen abzufangen, Rundzellen und Prismatische Zellen haben dafür ein Ventil im Deckel des Pluspols von wo es abgesaugt wird. Erst nach diesem Prozess wird das Gehäuse final und luftdicht versiegelt. Die Zelle ist jetzt fertig und wird noch einigen Tests unterzogen. Während mehrerer Lade- und Entladevorgänge wird der Verlauf von Spannung, Stromfluss und Temperatur gemessen sowie eine mechanische Prüfung der Verformung und Ausdehnung des Gehäuses durchgeführt. Einzelne Zellen werden im Anschluss wieder zerlegt, um auf Kristallstruktur-Ebene zu prüfen, ob die Alterung und der Kapazitätsverlauf plangemäß verlaufen. Die Testergebnisse fließen in ein Software-basiertes Simulations-Modell, aus dem man Verbesserungen für kommende Zellgenerationen ableiten kann.
Die Produktion von Akkuzellen bietet drei große Herausforderungen:
- Die Kosten für das Gewinnen und Verarbeiten des Aktivmaterials insbesondere auf der Kathode müssen gesenkt werden (Cobalt, Nickel und Mangan).
- Der Wasserbedarf für das Herstellen des Slurry für die Elektroden muss kontinuierlich gesenkt werden
- Der Trocknungsprozess benötigt immer noch viel Energie und Zeit und treibt damit die Herstellungskosten.
Dem gegenüber stehen die drei großen Geheimnisse, durch die jeder Zellhersteller versucht, seine Wettbewerber abzuhängen:
- Die Zusammensetzung des Aktivmaterials insbesondere auf der Kathode (sog. Zellchemie)
- Die speziellen kostensenkenden Maßnahmen bei dem Herstellungsprozess über alle Schritte
- Den genauen Vorgang der Erweckung der fertigen Zellen
Die Hersteller investieren massiv in die Forschung auf all diesen Ebenen und es ist in den nächsten Jahren mit signifikanten Fortschritten zu rechnen. Angesichts der Tatsache, dass die batteriebetriebene Elektromobilität ihren Durchbruch erlebt, herrscht im Umfeld der Zellhersteller eine regelrechte Goldgräberstimmung.
Quelle: https://www.pem.rwth-aachen.de/global/show_document.asp?id=aaaaaaaaaaoqixv
Bauformen
Im Bereich der Produktion von Akkuzellen haben sich im Wesentlichen drei Gehäuseformen durchgesetzt, die je nach Anwendungsfall gewisse Vorteile aber auch Nachteile mit sich bringen.
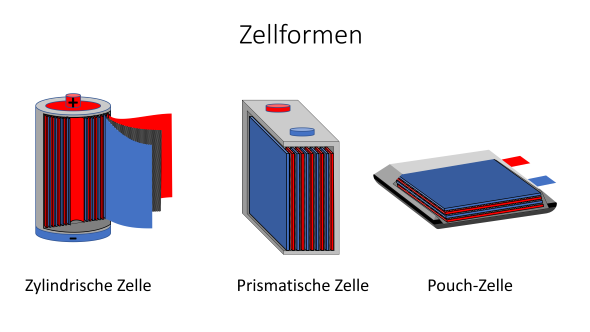
Rundzellen sind zylinderförmig und haben an den Enden jeweils einem Pol. Die Elektrodenfolien zusammen mit dem Separator zu einer Rolle aufgewickelt, was eine kostengünstige Produktion ermöglicht. Die Benennung der Zellen erfolgt als 4 oder 5-stellige Zahl. Dabei bedeutet z.B. die Zellenbezeichnung „18650“, die Zelle besteht aus einem Zylinder von 18mm (Millimeter) Durchmesser und 650 zehntel Millimeter – also 65mm Höhe. Der Zweite Wert wird oft als zehntel Millimeter angegeben, weil diese Benennung auch bei flachen Knopfzellen verwendet wird. Beispiel Knopfzelle CR 2032: 20mm Durchmesser, 3,2mm hoch. Das zylindrische Gehäuse verhält sich bei Ausdehnung sehr formstabil und robust. Die ansonsten weit verbreiteten Rundzellen kahmen zu Beginn der Elektromobilität zunächst nicht in Frage, weil sich die runden Zylinder nicht lückenlos aneinanderreihen lassen und damit im Platzverbrauch ungünstig sind. Insbesondere Tesla hat es aber geschafft, diesen Nachteil mit einer besonders effizienten Zellchemie auszugleichen und dafür die niedrigen Produktionskosten der Rundzellen zur Geltung zu bringen. Die unvermeidbaren Lücken zwischen den Zellen werden in dem Fall für die Wärmeabfuhr genutzt.
Prismatische Zellen haben die Form eines Quaders oder Blocks. Die Pole sind an der oberen Seite herausgeführt. Durch die viereckige Form lassen sich die prismatischen Zellen sehr gut lückenlos aneinanderreihen, was wiederum die Wärmeabfuhr erschwert. Das Gehäuse ist ebenfalls stabil, kann sich bei einer Ausdehnung allenfalls etwas leichter ausbeulen als eine Rundzelle. Die Elektrodenfolien werden als ca. 80 einzelne Schichten oder in Fächerform (Z-Stapel) mitsamt dem Separator aufeinandergestapelt. Das Verfahren ist dadurch aufwändiger als das Wickeln bei der Rundzelle und deshalb teurer. Bei Elektroautos kommt die prismatische Zelle oft zum Einsatz, weil sie eine hohe Packungsdichte im Battery Pack ermöglichst und leicht zu verarbeiten ist.
Die Pouch-Zelle (Coffee Bag) hat kein festes Gehäuse, sondern eine weiche Außenhaut aus einer robusten Aluminiumfolie. Dadurch ist die Zelle besonders günstig, leicht, kann dicht in einem Battery Pack verbaut werden und hat eine gute Wärmeableitung. Die Elektroden werden als Stapel verbaut und die Pole als Fähnchen aus dem Gehäuse herausgeführt. Pouch Zellen können dem Innendruck nicht gut standhalten. Damit sie für den Einsatz in einem Elektrofahrzeug ausreichend gesichert sind (Mechanische Integrität), müssen sie in ein Modulgehäuse verbaut werden. Ansonsten findet man Pouch-Zellen auch in vielen elektronischen Alltagsgegenständen wie Smartphones.
Die beigefügte Tabelle erlaubt einen übersichtlichen Vergleich der Formate.
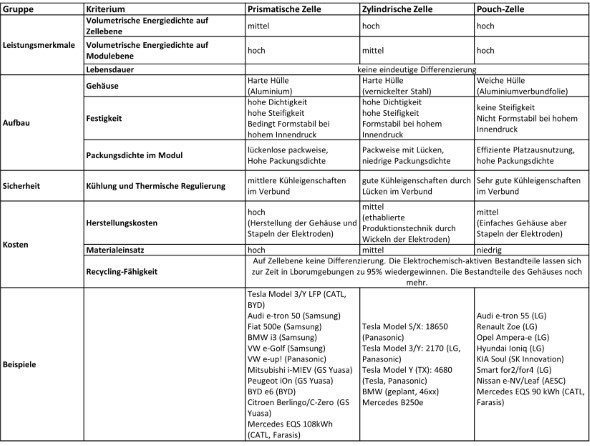
Die 4680er Zelle von Tesla
Beim Battery Day im September 2020 hat Elon Musk mit seinem Team das Konzept der 4680er Zelle vorgestellt. Auf den ersten Blick handelt es sich nur um eine größere Rundzelle mit 46mm Durchmesser und 80mm Höhe. Ziel ist aber die Steigerung der Produktionszahlen durch Senkung der Kosten bei gleichzeitiger Erhöhung der Leistungsfähigkeit und der Reichweite. Folgende Verbesserungen wurden seinerzeit angekündigt:
- Zell-Design: Das größere Gehäuse senkt die Materialkosten, erhöht die Leistungsdichte (5x mehr Energie). Durch die Anordnung der Pol-Tabs auf den Elektroden verbessert sich der Innenwiderstand und erlaubt eine Steigerung der Leistung beim Beschleunigen und beim Laden (6x mehr Leistung, siehe Bild). Dabei werden 14% der Kosten gesenkt und 16% Beitrag zur Steigerung der Reichweite erzielt.
- Neuer Herstellungsprozess: Tesla führt als erster Fahrzeughersteller die Pulverbeschichtung des Aktivmaterials der Elektroden ein. Das spart große Teile des Wasserbedarfs und es spart den Trocknungsprozess in Bezug auf Zeit, Energiebedarf (10%) und Platzbedarf in der Produktion (10% Einsparung); insgesamt 18% Kosteneinsparung.
- Neues Anodenmaterial: Die neue Anode besteht nicht mehr aus reinem Grafit, sondern hat einen Silizium-Anteil. Sie speichert bis zu 9x mehr Lithium wie reines Grafit. Das erhöht die Reichweite um weitere 20% und senkt die Kosten um 5%.
- Neues Kathodenmaterial: Die neue Zellchemie hat einen erhöhten Nickel-und Mangan Anteil und dafür weniger Cobalt. Das spart 12% Kosten und bringt 4% mehr Reichweite.
- Verbauen als Structural Battery Pack (Cell-To-Body): Durch die neue Bauweise des Battery Packs reduzieren sich die Kosten um weitere 7%, 14% mehr Reichweite. Dazu später mehr.
Während andere Zellhersteller fast täglich große Revolutionen aus ihren Laboren verkünden, hat Tesla inzwischen die Produktion der ersten Chargen der 4680er-Zelle im Werk in Austin, Texas aufgenommen. Diese scheinbar kleine Revolution hat immerhin zu einer Kostenreduktion pro Zelle von 56% und zu einer Erhöhung der Fahrzeugreichweite von 54% geführt. Diese Verbesserung ist in der Realität angekommen und wird bei den ersten Model Y aus Texas eingesetzt. Als nächstes ist damit zu rechnen, dass die 4680er-Zellen im Tesla Semi Truck und im Cybertruck einbaut werden.
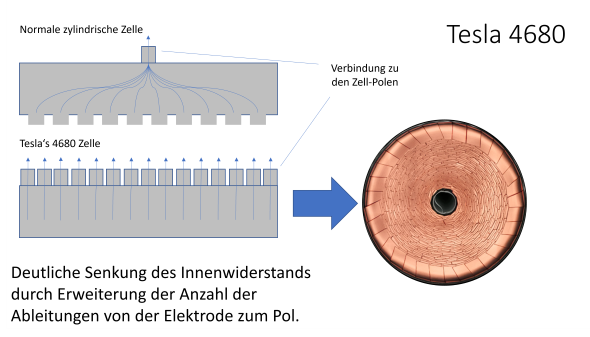
Arten von Zell-Packs
Unabhängig vom Aufbau der Zellchemie und der Zellform kann der Fahrzeughersteller auch beim Verpacken der Zellen im Fahrzeug einen signifikanten Einfluss auf die Energiedichte, das Zusatzgewicht und die Herstellungskosten nehmen. Bei Fahrzeugen, die von einer Verbrenner-Plattform abgeleitet sind, werden die Akkuzellen meistens in modularen Baugruppen untergebracht, die man im Fahrzeug an den Stellen positioniert, wo sonst der Verbrennungsantrieb eingebaut war. Das ist zum Beispiel der ehemalige Motorraum oder der Raum für den Kraftstofftank. Für den Batteriebetrieb konzipierte Elektroautos tragen den Akku meistens in einem flachen Gehäuse am Unterboden zwischen den Achsen. Deshalb spricht man auch von der Skateboard-Bauweise. Der damit verbundene niedrige Schwerpunkt begünstigt nicht nur ein sicheres Kurvenverhalten, sondern man kann die gewonnenen Freiräume innerhalb der Karosserie vollständig als Nutzraum verwenden. Aber auch bei dieser Bauweise gibt es inzwischen verschiedene Varianten, die sich bezüglich Kosteneffizienz und Variabilität unterscheiden.
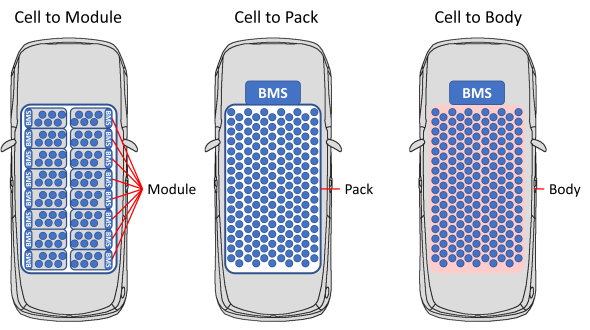
Bei den meisten batteriebetriebenen Elektroautos wurden die Akkuzellen in kleinere handliche Module verpackt. Jedes Modul beinhaltet die mechanische Fixierung der Zelle sowie das entsprechende Temperatur-Management zum Kühlen oder Vorwärmen. Gleiches gilt für das Battery Management System (BMS), eine Steuerplatine, die den thermischen und elektrischen Zustand der Zellen im Modul überwacht und bei Bedarf Spannungen, Ströme und Temperaturen reguliert. Die Zellen sind im Modul nach einem bestimmten Verfahren in serielle Stränge angeordnet, diese sind wiederum parallel geschaltet zum Erreichen der gewünschten Modulspannung. Module können im Auto verteilt eingebaut werden oder in einem Gehäuse angeordnet werden, dem Battery Pack. Weil das Modul die kleinste austauschbare Einheit darstellt, nennt man diese Technologie Cell-to-Module.
Die Elektrofahrzeuge der aktuellen Generation haben in den letzten Jahren vielfach hohe Kilometerleitungen ohne Akkuprobleme erbringen können. Die Austauschbarkeit der Einzelmodule musste nur selten zur Anwendung kommen. Dafür ist der hohe Materialeinsatz für die Modulbauweise vor allem mit Gewicht und Kosten verbunden. Deshalb werden bei vielen Fahrzeugen Akkus verbaut, bei denen die Zellreihen direkt in das Battery Pack eingesetzt werden. Das führt zu einer verbesserten Nutzung des Bauraums verbunden mit geringeren Kosten für den Materialeinsatz. Auch das Temperatur-Management sowie das BMS werden zentralisiert und somit die Komplexität insgesamt verringert. Die schlechtere Reparierbarkeit wird angesichts der geringen Ausfallquoten bewusst in Kauf genommen. Zum Austausch wird das gesamte Pack vom Unterboden demontiert und durch ein neues ersetzt. Die alten Packs gehen danach zurück an den Hersteller zur Reparatur oder zum Recycling. Diese Technologie wird als Cell-To-Pack bezeichnet und ist im Jahr 2022 bei vielen Herstellern der aktuelle Stand der Technik.
Die nächste Generation des Zellverbunds wurde von Tesla eingeleitet. Dabei wird das Battery Pack nicht mehr als eigenständige Baugruppe von unten an den Boden geschraubt, sondern das Pack selbst ist der Unterboden und somit tragender Teil der Karosserie. Man nennt diese Technologie Cell-To-Body oder Structural Battery Pack. Das gesamte Pack inklusive der Zellen, der Kühlleitungen und des BMS werden durch eine hartschaumartige Struktur miteinander in einem Metallgehäuse vergossen. Die innenliegenden Teile sind nicht mehr zugänglich. Diese reparaturunfreundliche Methode spart zusätzlich Kosten und Gewicht, was sich wiederum positiv auf den Verbrauch und die Reichweite des Fahrzeugs auswirkt. Die verbauten Zellen müssen den höchsten Entwicklungsstand bezüglich der Zellchemie haben und sind auf eine Lebensdauer von mehr als 2000 Ladezyklen oder 1 Mio. Meilen (1,6 Mio. Kilometer) ausgelegt. Der Akku wird die typische Lebensdauer des Fahrzeugs überdauern. Nur im Notfall wird zum Austausch die mittlere Bodengruppe entnommen, welche zu diesem Zweck verschraubt und nicht verschweißt ist.
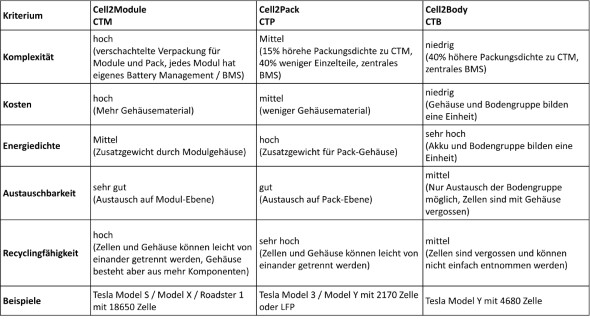
Fazit
Die Konzeption und die Produktion der Akkuzellen haben beim batteriebetriebenen Elektrofahrzeug eine ähnlich zentrale Bedeutung wie die Entwicklung des Motors beim Verbrenner. Angesichts der Tatsache, dass die Entwicklung noch am Anfang steht, lässt sich heute nur erahnen, in welche Bereiche wir in den nächsten 10 Jahren vordringen in Bezug auf Herstellungskosten, Leistungsdichte und Haltbarkeit.
Bei modernen Fahrzeugen laufen die Zellen stets unter kontrollierten Bedingungen und unter Einhaltung der strengen Sicherheitsanforderungen. Zusammenfassend kann man sagen, dass für den normalen Autofahrer der Produktionsprozess, die Zellform und das Packungsverfahren bei der Fahrzeugwahl keine Rolle spielen. Nach den bereits umfangreichen Erfahrungen der letzten Jahre haben die Fahrzeughersteller die Akkus ihrer Fahrzeuge längst so konzipiert, dass man über eine lange Distanz seine ungestörte Freude am Elektroautofahren haben wird.
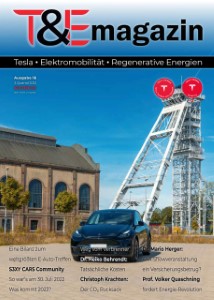
Das T&Emagazin
Der Artikel ist erschienen in der Ausgabe 16 (Oktober 2022) des T&Emagazins.
(Online Lesen)
Das T&Emagazin entsteht durch Beiträge der Community und behandelt Themen rund um E-Mobilität und Energiewende.
Das T&Emagazin ist an rund 350 Auslageorten im deutschsprachigen Raum kostenlos zu finden. Interessierte, die das Heft bequem zuhause im Briefkasten haben wollen, können es jedoch auch gegen Übernahme der Versand- und Portokosten über den T&Eshop anfordern. Wer 5, 10 oder auch 20 Hefte haben möchte, kann bequem entsprechende Pakete ordern. Zudem besteht die Möglichkeit, das T&Emagazin in Wunschmenge dauerhaft zu abonnieren.